Nickel and Cobalt
Aurora has nickel and cobalt assets that are located north of the provincial capital of Ambon, throughout the western side of Seram Island (all except the coal mining concession that is on the far right of the below map).
The nickel-cobalt mining locations have been explored over the previous decades, with initial surveys by the Indonesian state owned mining holding (ANTAM) and subsequent geophysical surveys and trenching/drilling by the private company that secured the mining licenses which Aurora now holds.
Nickel: 1.6 - 2.7 %
Cobalt: 0.1 - 0.47 %
Uses of Nickel and Cobalt:
Nickel is used as a coating of stainless steel, making aliases of metals such as monel, nicron and alkino, and nickel powder is used as a catalyst for hydrogen products in the manufacture of margarine. Based on its flexible nature, unchanging when exposed to air, its resistance to oxidation and its ability to maintain its original properties at extreme temperatures, nickel is widely used in many commercial and industrial applications. About 70% of nickel production is used for stainless steel production, while the remainder is used for various industrial uses, such as:
-
Stainless steel (steel protector)
-
Rechargeable batteries
-
Manufacture of alnico magnets (magnetic alloys consisting of aluminum (Al), nickel (Ni) and cobalt (Co))
-
Installation of a salt removal process to convert sea water into fresh water (in the form of copper-nickel alloy)
-
As a catalyst for hydrogenating vegetable oil or making it solid (in the form of very fine nickel)
-
Copper protector
-
Electric light wires
-
Fat catalyst
-
Agricultural fertilizer
Cobalt is obtained from ores as a sulfate in many cases.
Hydrated cobalt (II) sulfate is used in the preparation of pigments, as well as in the manufacture of other cobalt salts. Cobalt pigment is used in porcelains and glass. Cobalt (II) sulfate is used in rechargeable batteries and electroplating baths, sympathetic inks, and as an additive to soils and animal feeds.


Mining
We carry out mining operations using the most effective technologies and equipment, with the key to our success being the high qualification of our employees, their experience and ability.
Long lead item procurement is commencing, including:
• Generators
• Fabrication of special material equipment
Infill drilling program to better define areas of higher grade cobalt is being prepared.
Early construction works are being prepared, including:
• Mining camp
• Water/power utilities
• Site infrastructure
• Earth works
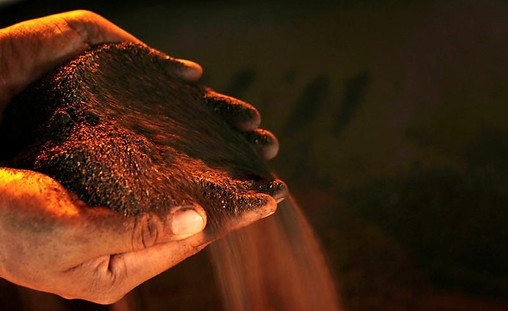
Hydrometallurgy
We carry out three major functions – laterite ore processing, mixed nickel-cobalt hydroxide processing, and nickel and cobalt refining.
The ore processing section comprises receival of shipments of nickel laterite ore, blending, drying, milling and reduction roasting at about 750°C using Herreshoff multiple hearth furnaces. The reduced ore is cooled and then leached in ammonia ammonium carbonate liquor at atmospheric pressure to selectively dissolve nickel and cobalt. Product liquor (PL, typically 10 to 12 g/L Ni and 0.6 g/L Co) is separated from the tailings solids in an eight thickener washing circuit. Tailings slurry is steam stripped to recover ammonia prior to disposal in storage ponds.
The PL from the ore processing section contains excess ammonia, part of which is utilised to dissolve further nickel and cobalt in the mixed nickel-cobalt hydroxide processing section. The resultant concentrated product liquor (CPL, typically 23 g/L Ni and 1.1 g/L Co) is separated from the residual solids (mainly manganese and magnesium carbonates), which are sent to the washing circuit in the ore processing section.
In the metal refining section of the refinery, the remaining excess ammonia in the CPL is removed by controlled steam stripping, enabling nickel to be separated from cobalt using an ammoniacal solvent extraction (ASX) technology. Nickel is selectively extracted, and then stripped from the nickel-loaded solvent using concentrated ammonia ammonium carbonate solution. The resultant nickel loaded strip liquor (Ni LSL, typically 75 to 80 g/L Ni, 0.05 g/L Cu and 0.02 g/L Co) is further purified by selective copper sulfide precipitation to 0.001 g/L Cu, and then steam stripped to precipitate basic nickel carbonate solids (BNC, typically 52% dry wt Ni). The slurry is dewatered using thickeners and pressure filters.
The raffinate from the ammoniacal solvent extraction circuit (typically 1.0 g/L Co and 0.02 g/L Ni) is sulfided using ammonium hydrosulfide solution. Cobalt sulfide solids are separated using a thickener, allowing the barren liquor to be recycled to the washing circuit in the ore processing section. Cobalt sulfide solids are oxidatively dissolved using air and oxygen to produce a crude cobalt sulfate solution, from which the zinc, iron, nickel, sulfur, magnesium and calcium impurities are selectively removed using three solvent extraction stages and one ion exchange stage. The resultant high purity cobalt ammine solution (typically 65 g/L Co and <0.001 g/L Ni) is steam stripped to precipitate chemical grade cobalt oxide/hydroxide solids. The slurry is dewatered using a thickener, pressure filter and fluid bed drier.
Processing
Our nickel-cobalt laterite ore is proceeded using a proprietary hydrometallurgy process, to derive nickel- and cobalt-sulfates, which are then directly used in the manufacture of rechargeable battery cells.
The process is uniquely designed to utilize seawater, which is readily available at the site of our mining concessions, and is optimized for the production of rechargeable battery precursors, rather than for large-scale metallurgy. This allows the construction of a smaller scale plant, which is specifically targeted at the more profitable sulfate production instead of being oriented towards the declining metallurgical market.
The tropical location of our concessions and plant, with constant 28°C - 34°C temperatures, provides additional energy savings during the hydrometallurgy process.
Detailed engineering and design for process plant and associated infrastructure is being prepared.
Long lead item procurement is commencing, including:
• Acid plant
• Sulphur plant
• Generators
• Fabrication of special material equipment
Early construction works are being prepared, including:
• Construction camp
• Water/power utilities
• Site infrastructure
• Earth works
