Production of NMC Powder
The process for the production of the desired oxide (LiaNixMnyCozO2) begins with the reaction of solutions of the substrates, e.g., MSO4, M = Ni, Mn, or Co, reacting with a carbonate or a hydroxide to produce the corresponding carbonate or hydroxide co- precipitates.
MSO4 + Na2CO3 = MCO3↓ + Na2SO4
MSO4 + 2NaOH = M(OH)2↓ + Na2SO4
The dried carbonate powder is then mixed with lithium carbonate or hydroxide and calcined to produce the desired oxide.
NiCO3 + MnCO3 + CoO3 + Li2CO3 + O2 → LiaNixMnyCozO2 + CO2
The solution of sulfates (dissolution in mixers not shown) is reacted with the carbonate solution in a continuous stirred tank reactor (CSTR) maintained at a desired pH with the addition of a hydroxide solution in a reactor maintained at 45 to 95°C. The required residence time in the reactor is typically 10 hours. The reaction itself is exothermic, but the heat needed to elevate the temperature of the feeds to the reaction temperature for the base case scenario of 95°C is nearly three times the heat of reaction. The thermal management is simplified by introducing the feed solutions at a temperature lower than that of the reactor such that the heat of reaction allows the reactor to be maintained at the desired or specified temperature.
The product stream, a slurry of solid precipitates in a sulfate solution, is phase separated, and then filtered and washed several times. The filtration may be done in a rotary vacuum filter followed by drying in a spray dryer. The dried powder is milled to the desired particle size, and then mixed with lithium carbonate. The mixture is then sintered in a kiln or furnace at temperatures of 500-1000°C.
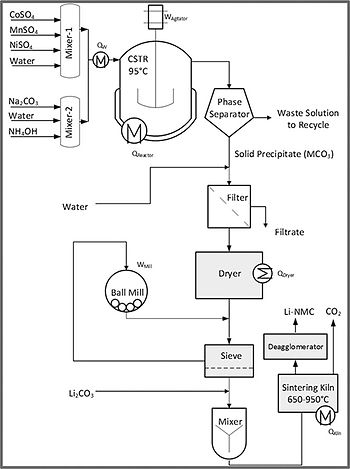